Poolside peaks: Crafting a diving experience from GFRC rock
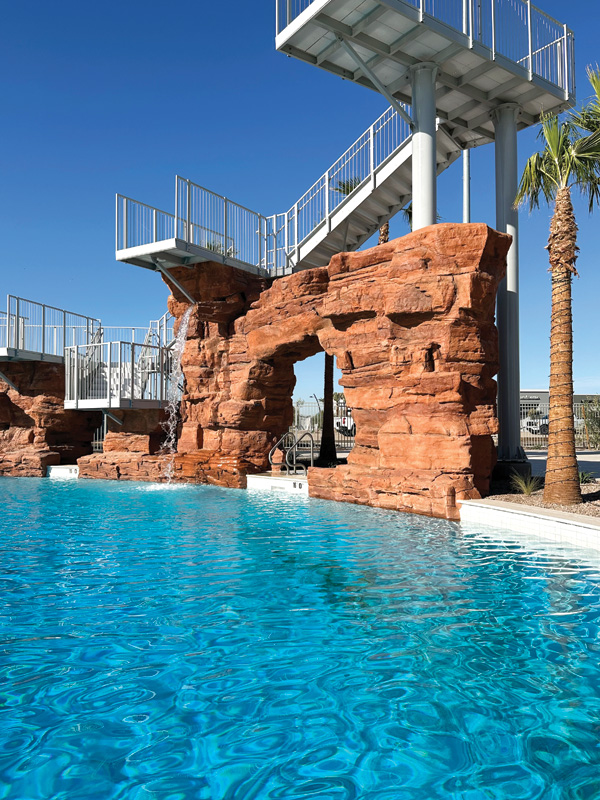
A new multi-use development recently opened its doors to the public in December. Cannon Beach is a $45 million, 1.8-ha (4.5-acre) water park with exciting attractions. The site boasts four cliff jumping platforms ranging from 1.8 to 7.9 m (6 to 26 ft) in height, multiple restaurants, a skate park, an infinity wave pool, and a 0.8-ha (2-acre) surf lagoon with 11,356,235 L (3,000,000 gal) of water. While the large surf wave pool is impressive, the most stunning visual feature of the facility is the series of cliff jumping platforms, which use cast concrete and faux rocks to replicate the natural rock arches and spire formations of Arches National Park in Utah.
The entire structure was fabricated in Texas at the authors’ facility, then shipped in pieces to its final destination, where it was assembled and installed in place.
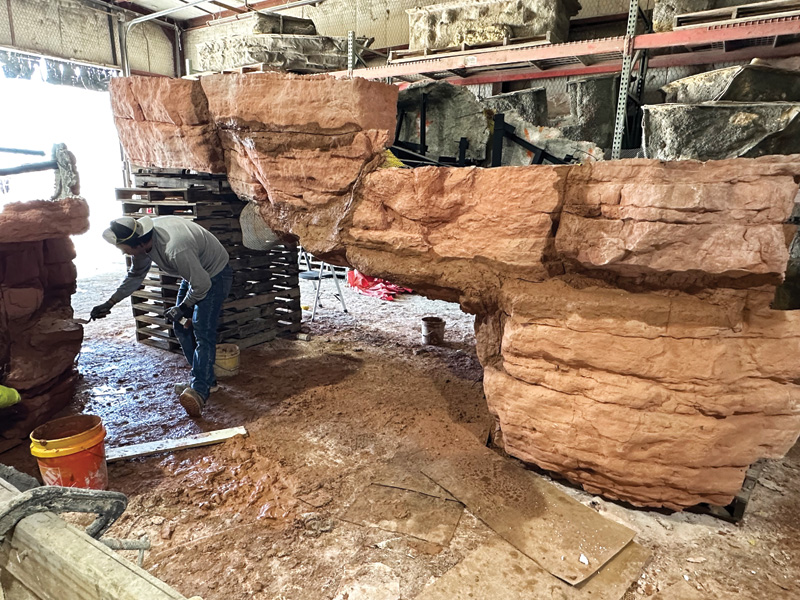
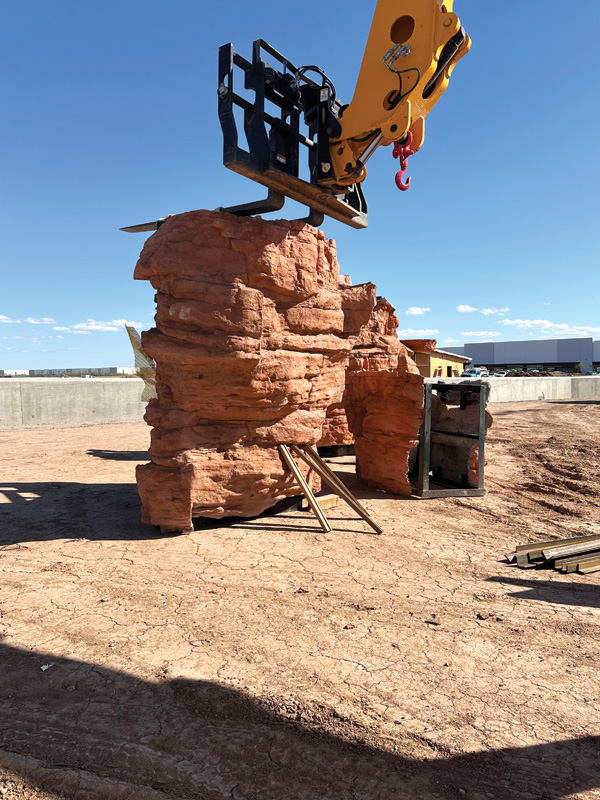
The inspiration, design, and realization of this glass fibre-reinforced concrete (GFRC) rock structure were driven by the creativity and expertise of the lead designer, an avid rock climber who takes annual trips to Moab, Utah. The designer brought the cliff diving platforms to life with expertise drawn from his experience as a rock climber. Located in Mesa, Arizona, this facility officially opened in December 2024.
The rock was initially designed to reflect the Sedona sandstone esthetic, but the concept evolved to draw inspiration from the iconic rock formations in Moab, Utah. Throughout the design process, the rock structures underwent multiple revisions, both structurally and in quantity. Additional rock features were incorporated to bring more “life” and character to the park. This included placing rocks at the end of every lagoon feature, such as benches, stairs, and dividers between the wave and lagoon pools. The goal was to ensure the rock elements were distributed evenly across the diving lagoon for a balanced, natural esthetic.
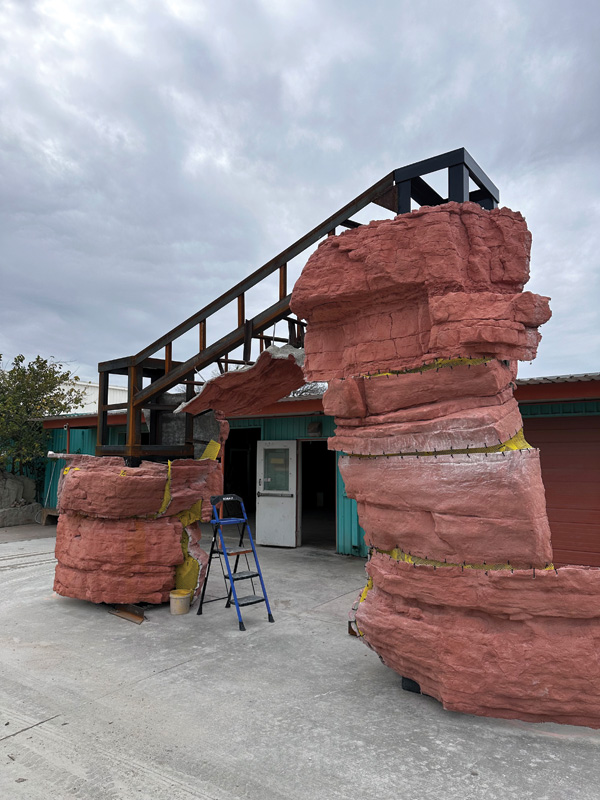
The result is a stunning integration of natural-inspired elements that complement the lagoon’s features, adding depth and character to the
overall experience.
The concept and inspiration
The authors’ company has collaborated with H2O Designs Inc. on multiple aquatic projects, and H2O Designs frequently asks them to contribute to creating appealing surrounding esthetics.
H2O Designs emphasized their desire for more rock elements. Similar to other projects the two companies have collaborated on, cast-concrete rock proved to be an effective solution. The initial concept drawings specified diving tower poles covered in Utah-style rock, featuring horizontal strata lines and a red hue.
Inspired by this vision, the lead designer proposed enhancing the design by connecting the spires with an elegant archway reminiscent of Utah’s “Delicate Arch,” a renowned natural wonder in Arches National Park near Moab, Utah. This freestanding sandstone formation stands 16-m (52-ft)-tall and was shaped over millions of years by wind, water, and erosion forces. The idea resonated with the team, and they decided to move forward.
The decision to incorporate the arch as a centrepiece marked a turning point in the project, shifting the team’s focus toward designing and constructing this dramatic feature. The greatest challenge lay in the prefabrication process, where precision was crucial. Even a small error, such as being off by a foot, could have jeopardized the entire project. To address this, the team collaborated closely to ensure every aspect was executed with meticulous accuracy. A key breakthrough was developing the “clamshell” method, allowing the team to encapsulate the steel towers fully. This involved creating two C-shaped frames bolted together to form a complete circular structure, ensuring stability and functionality.
Challenges
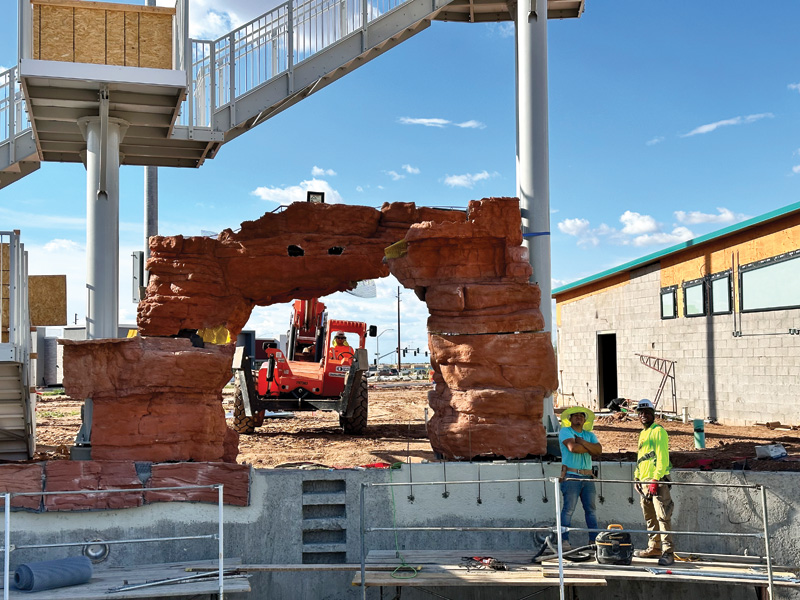
The creation and installation of the cast concrete rock structures presented several challenges, primarily because the faux rock components were fabricated in Seguin, Texas, and shipped to Mesa, Arizona, for installation. The process began with concept drawings developed into a detailed vision over three to four weeks. A site visit was conducted to visualize the space and take precise measurements, which were used in Texas to lay out the structure on the fabrication facility floor and establish a sense of scale.
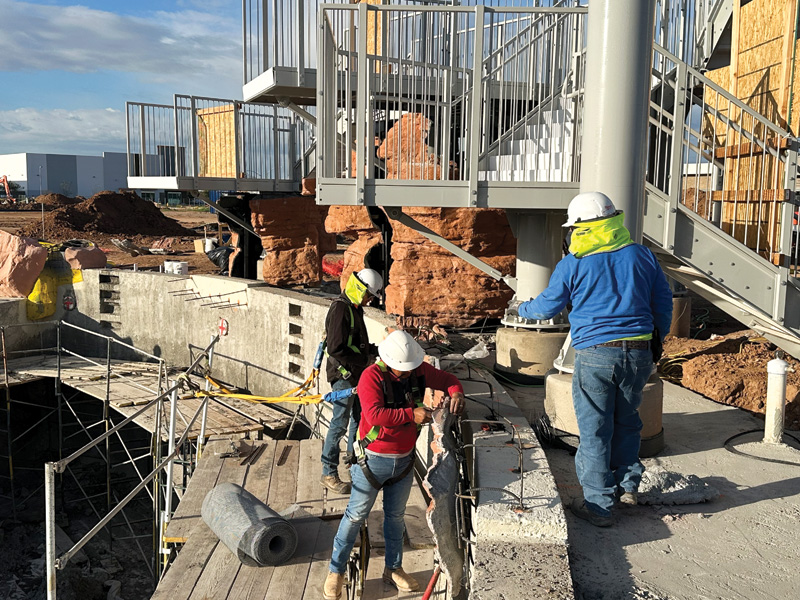
With the detailed concept and designs finalized, the team transitioned to the critical phase of prefabricating the rock structures, focusing on precision and durability. To ensure accuracy during prefabrication, foam blocks were cut into cylinders to replicate the bases of each diving platform. Measurements from the site visit were transferred to the fabrication floor, where the foam cylinders were carefully spaced to match the layout. The steel framework was constructed around these foam cylinders, ensuring the dimensions aligned perfectly with the on-site requirements. This meticulous process proved successful, as the rock structures fit seamlessly during installation.
For added safety and longevity, the framework was constructed using 127 x 127 x 9.5 mm (5 x 5 x 0.375 in.) angle iron coated with epoxy to protect against weathering and environmental wear.
The arch was a significant undertaking, comprising GFRC pieces weighing between 1,360 and 1,810 kg (2,998 and 3,990 lb) each. One of the poles was encased in a clamshell-like structure, and the entire arch weighed more than 5,900 kg (13,007 lb). The project required careful planning to achieve seamless on-site installation.
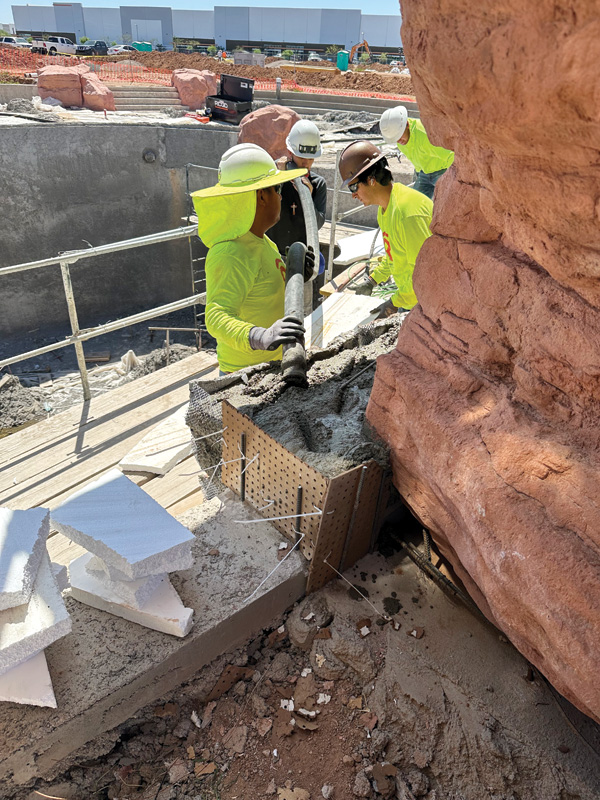
A telehandler, an extended-reach forklift with a 12.2-m (40-ft) boom, was used to maneuver the pieces into place to transport the rock structure. Each component was equipped with 15.8-mm (0.625-in.) holes and hoisting eyelets, which were lifted using straps rated for heavy loads. The pieces were secured onto a flatbed truck, transported to Arizona, and unloaded in the same manner for on-site assembly.
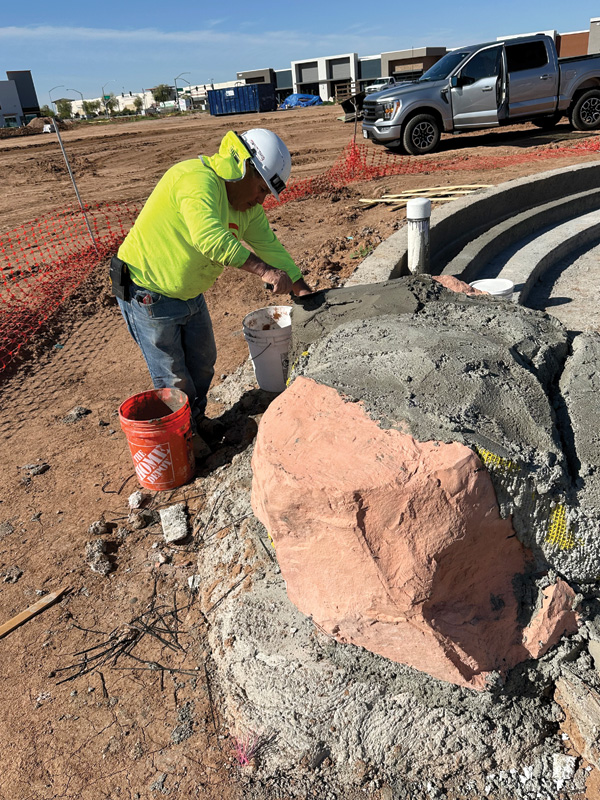
At the project site, the structure was placed onto concrete footings made to precise specifications by Shasta Pools, the pool contractor on the project. The GFRC frame structures were bolted, welded, and secured onto the footings. The final design gives the appearance that the rock formations support the diving platforms, although separate poles manufactured by SPLASHTacular support the platforms themselves. This seamless integration of the rock formations with the diving platforms showcases the precision and expertise needed to bring the project to life.
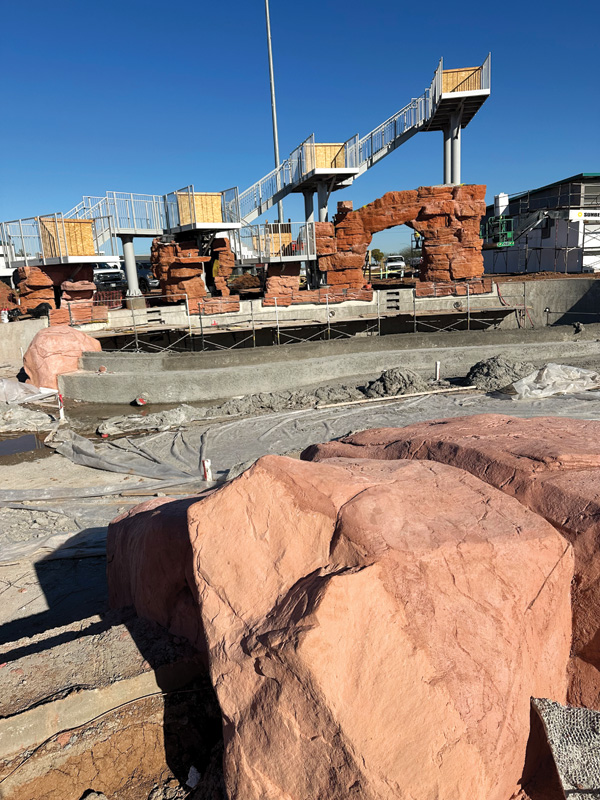
Final touches
The primary colour of the GFRC rock structures was applied during fabrication at the Texas facility, using an integral colour referred to as “Sedona-Red.” This colouring process was completed during the casting of the concrete, ensuring consistency throughout the structure. The seams and joints of the rock features were also pre-finished at the facility, so most of the work, including the colouring, was finalized before shipment. Stains were applied to these seams to enhance the highlights of the rock feature. An antiquing process was also used to bring out cracks with reddish-brown tones, adding depth and a natural geological appearance.
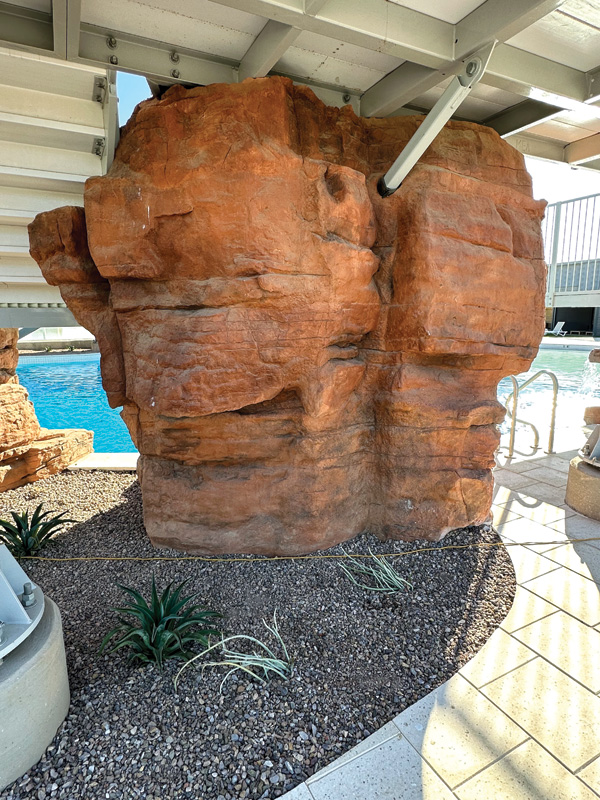
With the structural components completed and assembled, attention turned to the finishing details that would bring the rock formations to life with realistic colouration and texture. The precast panels were fabricated with integral colour, achieving the Sedona red hue consistent with the design vision. Additional colouring techniques were employed to enhance the rock formations’ visual depth and geological realism. Acrylic stains were applied to create greater dimension, with antiquing colours, such as black-grey, added to accentuate shadows within the cracks. A reddish-brown stain was also used to deepen the red tones, further emphasizing the natural appearance of the rock surfaces. These finishing touches added texture and complexity, resulting in a lifelike representation of natural geology.
Beyond the large spires and arches of the diving platforms, additional faux rocks were incorporated into the facility to create a cohesive esthetic. Underwater and in-water boulders were strategically placed, defining areas such as the edges of staircases and the ends of benches. These rocks differed from the GFRC used in the arches and were instead the traditional faux-rock style, where rebar is used with real-rock casting that holds the concrete in place. This was followed by filling the forms with 20.7 MPa (3,000 psi) concrete while vibrating it to eliminate voids. The rocks were then waterproofed and finished with a hand-textured integral colour mortar to provide visual continuity and match the overall esthetic of the facility. Many of these rocks were submerged, with approximately 406.4 mm (16 in.) visible above the waterline, blending seamlessly with the surrounding design.
The outcome
The client has met the GFRC rock installation at Cannon Beach with great enthusiasm. The attention to detail and careful execution of the design have resulted in a visually stunning centrepiece that complements the facility’s overall esthetic. For those looking to experience the GFRC rock formations firsthand, dive from the platforms, or enjoy surfing in Arizona, visiting Cannon Beach is a must-add to any list of vacation destinations.
Authors
Bruce Riley is the managing director of RicoRock Inc., a maker of cast-concrete rock, which includes component systems for building caves/grottos, waterfalls, and waterslide products for use in pool applications. Riley focuses on developing new products and managing commercial installations. He has built rock-type pools in southern California for more than 25 years and now uses this experience to design standard waterfall kits for the company. He can be reached via email at bruce@ricorock.com.
Zayvian Camacho is part of the RicoRock Inc. design and fabrication team, developing a new climbing wall and water features and working on commercial aquatic and non-aquatic construction projects. Camacho has studied landscape design and has overseen construction for dozens of unique cast concrete and artificial rock projects in backyards, hotel resorts, bowling alleys, zoos, and more. Camacho finds his rock construction work meshes perfectly with his passion for rock climbing. He can be reached via email at zayvian@ricorock.com.